Paddle Dryer
Paddle dryers are used to dry wet cakes, pastes, and thick slurries like sludge. The hollow paddles and jacket are heated by the flow of the heating medium, such as steam or hot oil, through them. After making contact with the paddles and container wall, the moist material dries.The paddles’ shape prevents product sticking and makes them self-cleaning. The moisture is removed from the product as it travels from one end to the other. Thermal fluid or steam is often used as the heating medium.
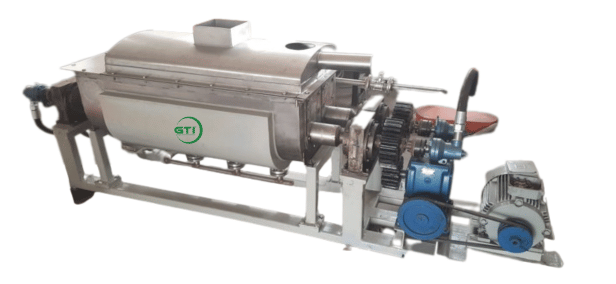
Paddle Dryer is used for following Applications:-
-
- Chemical: Salts, Catalyst, Brominated Organics, Cellulose, Starch
- Petrochemical: Solids Devitalisation
- Polymer and plastic: Polypropylene, Polycarbonate, Poly Phenyl Sulphide, PET, PTA
- Food: Flour, Beverage Powders, Confectionary Ingredients, Meat products, Biomass, Hemp, and More
- Mineral and metal: Metal powders, Metal carbonates, Sulphates and Hydroxides
- Waste Management: Sludge and Slurry
Advantages of Paddle Dryer:-
-
- High thermal efficiency
- Heat transfer medium does not come into contact with the product.
- Gas is not used to convey the product. Off-gas flow is minimal.
- Precise control of temperature
- Uniform product quality, thorough mixing and movement of the product
- Continuous process on a once-through basis
- High heat transfer area to process volume ratio – reduced floor space
- Pre-conditioning with recycle is typically not required.
- Easy to operate, requiring minimal attention
- Safer than direct drying when processing combustible material
- Simple durable design for easy and low maintenance
- Enclosed process contains odours and hazardous materials
Design:-
-
- Heat transfer areas from 20 to over 3000 square feet (5.6 to over 279 square meters) per dryer
- Heated with steam or circulated thermal fluid (hot oil)
- Cooled with water or water-glycol mixtures
- A two temperature-zone design is available
- Adjustable operating level increases process flexibility (turn-down)
- Process contact surfaces of carbon steel, stainless steel or alloy
- Surface finishes to meet process requirements (from mill to electro-polished)
- Available abrasion-resistant coatings
- Inert process during operation
- Robust equipment, designed for high torque and low operating speed
- Shafts, pillow block bearings, and drive components designed for long life under adverse conditions, ensuring long-term mechanical integrity.